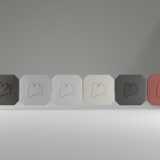
What’s at stake?
As resources become stretched and climate change accelerates, the need to reduce emissions is more urgent than ever. And increasingly a priority for governments, consumers and companies (including ours). Ambitious targets require us to decarbonise the entire value chain, from design to end of life, across all industries, especially automotive.
What can we do?
As well as focusing on Scope 1 & 2 emissions during manufacturing, this transition requires us to reduce Scope 3 emissions, upstream – when producing components and materials – and downstream across the entire product life cycle. Above all, this means finding or creating low-carbon alternatives designed for Scope 3 that can also be easily recycled.
Let’s dive deeper