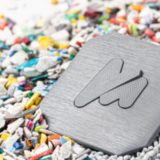
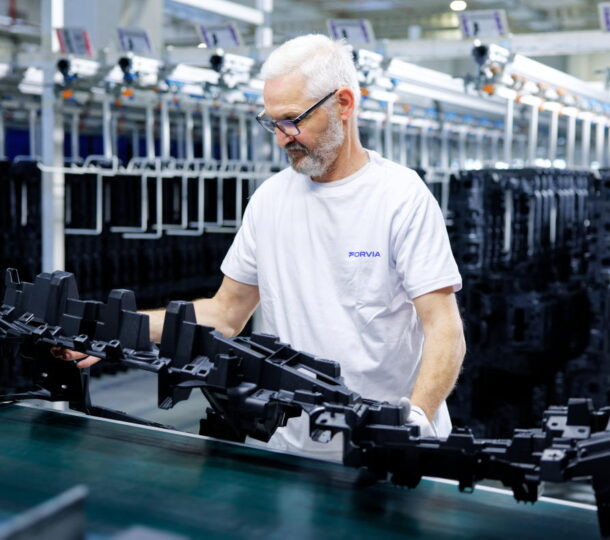
Ambitious recycled plastic content targets are essential to increase the circularity of the automotive sector…
How to take giant steps in developing high-performance materials – with tiny (carbon) footprints
01. What’s at stake?
In the context of dwindling resources and climate change, there is a growing push – an urgent need – to reduce emissions from governments, companies (including ours) and individuals. Targets are ambitious, requiring us to decarbonise the entire value chain, from design to end of life, whether in automotive or other industries.
Take ecological factors like CO2 emissions into account from day 1 including the choice of materials and impacts across the product’s entire life cycle.
Reduce emissions emitted during production and manufacturing processes, particularly through greater energy efficiency and less waste.
Find, create and reinforce ways to reuse and recycle products and materials, so they don’t end up in a landfill – contributing to a circular economy.
Many companies have started focusing on Scope 1 & 2, that is to say, emissions produced during manufacturing. But this (much needed) transition also involves upstream supply chain decarbonisation. This means homing in on emissions emitted when producing components and materials. For example, by shifting to low (or zero) carbon materials – that’s where companies like ours come in.
Downstream emission reduction also has a key role to play, and is particularly challenging. We need to ensure the entire life cycle aligns with decarbonisation goals including product use and end of life – ideally contributing to a circular economy where everything is reused. This means big changes in product design, business models and life-cycle management. And contributions from across all sectors.
Transport was responsible for a quarter of the EU’s total CO2 emissions in 2019 – 71.7% of that via our roads (European Environment Agency)
Transport is essential for all of us to go about our lives – for businesses too. We need to get from A to B, whether by train, plane or car. To reduce CO2 emissions, we can make vehicles more efficient, change the fuel or opt for less carbon-intensive materials (or all 3).
Progress has been made on multiple fronts. Combustion engines are increasingly efficient. While electric vehicle sales are on the rise: boosted by government subsidies in numerous countries and increasingly strict legislation – with an EU ban on the sale of new combustion-powered engines by 2035. Recycled and bio-based materials are also slowly making their way into vehicles.
But we need to pick up the pace.
Source : eurometal
Source : americanchemistry
Source : globalfueleconomy
02. Where we’re at?
developing polymers from renewable resources to replace fossil fuels – this shift lies at the very heart of our business model and vision! For example, we use biomass like CO2-sequestering hemp or recycled polypropylene. This significantly reduces the carbon footprint of our products – we’re aiming for an 85% reduction by 2030.
co-developing solutions with key recycling players, for example, contributing to PlastiLoop, Veolia’s integrated circular polymers platform that makes it easier to source recycled plastic.
working with local, like-minded suppliers to reduce transport emissions, support the local economy and keep everything close to home.
working with local, like-minded suppliers to reduce transport emissions, support the local economy and keep everything close to home.
optimise design and processes to limit the amount of material used during injection – cutting waste and energy requirements.
designing recyclable materials and adopting a single-material approach to make end-of-life recycling easier.
Ambitious recycled plastic content targets are essential to increase the circularity of the automotive sector…
This is the question that was asked, explored and turned upside down during the recent…
03. What’s next?
Companies from all sectors have started laying the groundwork for a less carbon-intensive approach. We’re keen to keep doing more. We can all contribute in different ways by working together across supply chains and sectors. Together, we can keep innovating new low-carbon bio-based or recycled materials. While also contributing to exemplary product life cycles to help close the loop through recycling and reuse.
At MATERI’ACT, we’re busy developing new materials with next-generation polymers and finding ways to integrate more recycled plastic and biomass. To help us get there, we’ve invested in cutting-edge technologies (including AI) to make our recycled materials more homogenous and efficient to meet demanding industry standards.
Alternatives to petroleum-based PVC and leather including bio-based knit fabric made from pineapple leaves. Vegan.…
Transforming biomass like hemp, pineapple fibres and oyster shells into shiny new materials.
We’re always looking for new partners and customers to help us create fossil-fuel alternatives
to high performance standards, which can be (and are) recycled
The road to net-zero and zero new plastic is going to get bumpy at times. But that’s the only road we care to take.
Wanna join us?
Pick a challenge you’d like to tackle with us.