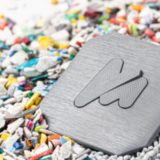
keeping feedstock sources close to production sites to reduce transport emissions. At MATERI’ACT, we work with local partners, for example, our APM joint venture with neighbouring agricultural cooperative Interval enables us to integrate natural hemp fibres and recycled plastics into our production lines – without needing to whizz around the world (or even across France).