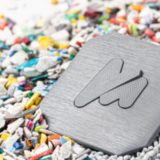
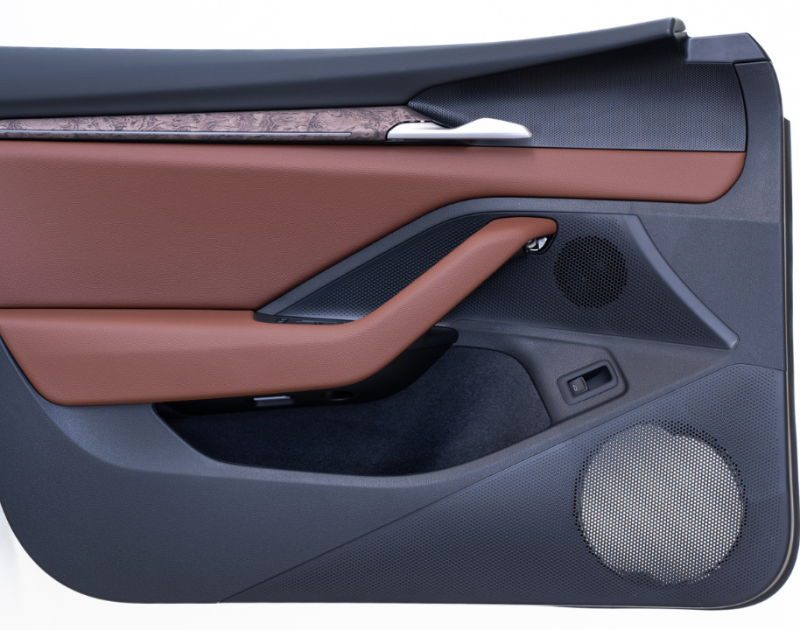
A recycled TPO solution engineered for thermo-covering door panels – combining recyclability, surface aesthetics and processability.
Recyclable, mono-material, and process-ready — our TPO range is designed to meet the industry’s toughest surface specs while simplifying complexity.
Up to 28% recycled Polyolefin content
Fully recyclable mono-material structure
Compatible with standard thermo-covering processes (IMG & PVF)
Meets high automotive standards for visible interiors
Weight saving, lighter than PVC
A recycled TPO solution engineered for thermo-covering door panels – combining recyclability, surface aesthetics and processability.
A TPO grade developed for vacuum-formed surfaces with deep geometries – for durable aesthetics and a step closer to circular design.
Let’s face it: surface materials are complex. Especially in automotive interiors, where multiple layers — lacquer, foam, adhesives — come together in tight tolerances. But if we want circularity to scale, we have to simplify. That’s exactly what our TPO range is designed to do.
By developing recyclable, Polyolefin-based solutions for the core layer — the compact layer — we enable OEMs to move toward fully mono-material skin structures. The result? Better recyclability, fewer material incompatibilities, and a more sustainable path forward for surfaces.
A typical TPO skin includes multiple layers:
A lacquer (top aesthetic finish)
A compact layer (structural support)
A foam layer (for softness and acoustics)
A primer or glue layer (to bond everything together)
At MATERI’ACT, we focus on the compact layer — the technical core that delivers structure, resistance, and compatibility with industrial processing. Our solution: Polyolefin base TPO + PP base foam + PP base glue. This combination enables a true mono-material, fully recyclable construction — no compromises.
Our TPO range currently includes two distinct technologies, each suited to a specific thermoforming process and design intent:
TPO – Thermoplastic Polyolefin: A soft-touch plastic blend, often used for dashboard skins and door panels.
IMG – In-Mold Graining: A forming process where texture is applied directly in the mold — great for high-end finishes
PVF – Positive Vacuum Forming: Uses vacuum to shape skins over foam, especially for parts with deep geometries.
Still sound niche? Don’t worry — the result is simple: beautiful, durable, recyclable surfaces.