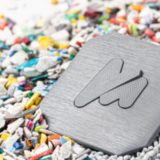
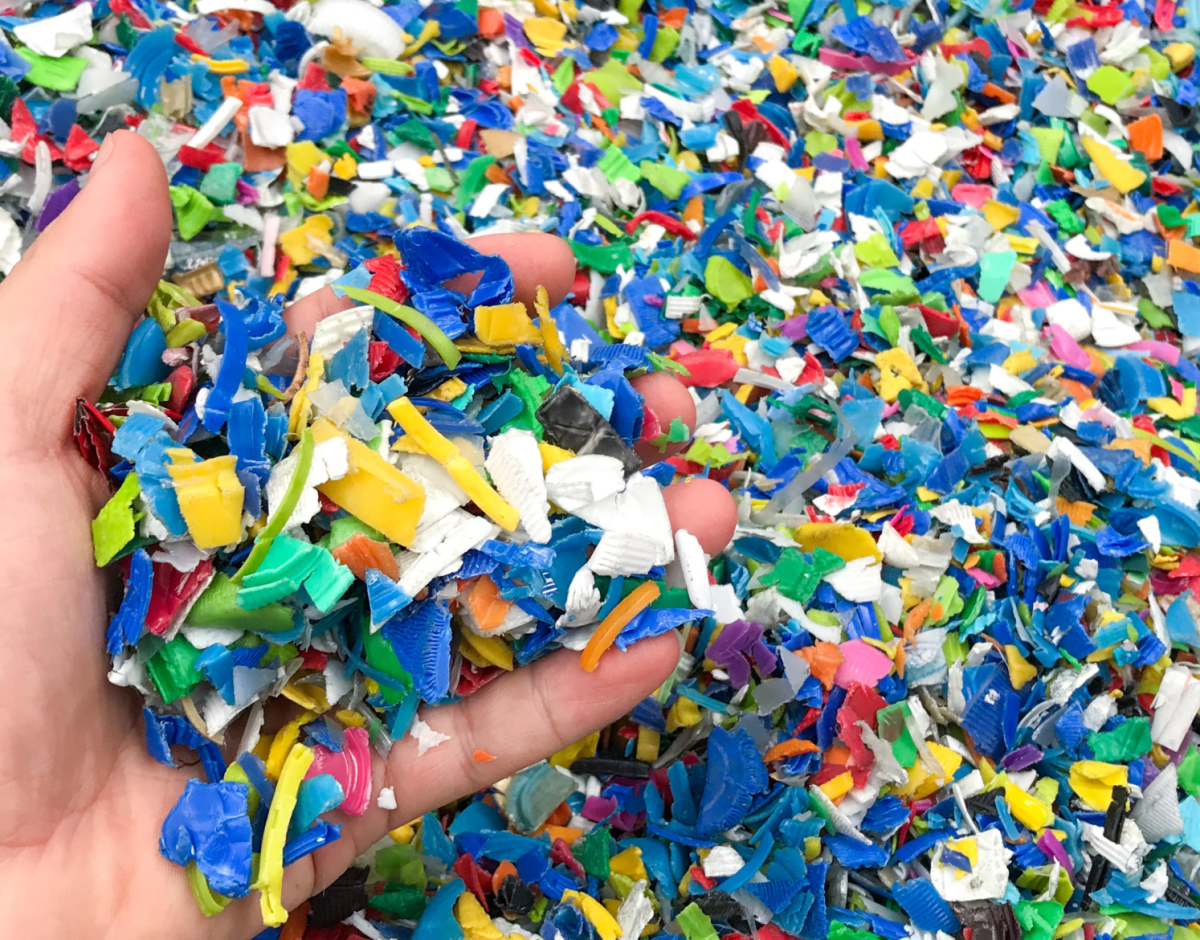
The properties of recycled materials are variable. But the end product needs to have constant, standardised qualities. Ready to take up the challenge, we realised that AI could play a key role in predicting formulations and adjusting production parameters on the go. To get there quicker and achieve better results, we reached out to the Auvergne-Rhône-Alpes Region for funding support and experts within the local ecosystem to bring complementary skills and experience on board.
Officially launched in May 2024 for a four-year period, the FAVIA project brings together 4 companies, all based in the Auvergne-Rhône-Alpes region. As well as our teams at MATERI’ACT, there’s also Aryballe that specialises in Volatile Organic Compound (VOC) sensors. While POLLEN Metrology boosts production with artificial intelligence software. Let’s not forget the Centre Technique Industriel de la Plasturgie et des Composites (IPC) that carries out research into plastics and composite materials.
Keen to support innovation and sustainability within the local ecosystem, Auvergne-Rhône-Alpes Region is providing invaluable support mobilising 3.6 million euros in European structural funds from the European Regional Development Fund (ERDF).
Let’s find out more from Michael Lemoine, FAVIA Technical Coordinator, Adaptative Formulations & Recycled Technologies Manager at MATERI’ACT.
Recycled materials are a world away from virgin materials. The variable input means that the characteristics can be different every time – which doesn’t go down well with customers! We need to ensure that each material we develop is stable and consistent, meeting demanding specifications. This means choosing the best possible formulation and then adjusting it with just the right quantity of ingredients during production. Using algorithms is a great place to start, but we wanted to take this further by using advanced sensors for digital sample analysis and automatic adjustments directly on the production line. That’s what makes this project so strategic – and exciting.
In my previous job, I’d already started looking at digital sample analysis to speed things up without needing to send the samples to a lab. So I was delighted to have the opportunity to investigate further.
We aim to have developed a solution capable of using sensors to digitally analyse samples, predict formulations and adjust extruder inputs in real-time to produce different kinds of materials based on recycled plastic (or biomass) – with the same characteristics every time. This would support decision-making, ensure consistent quality and reduce time to market.
As technical coordinator, it’s been an ambitious project. We needed to find the best ways to all work together – doing some work individually as a company and also sharing our findings, including quarterly technical committees. Being geographically close makes this a lot easier. In house, we have a small team of project managers and data scientists dedicated to this project, but working with our partners brings additional multidisciplinary skills and speeds things up too. The teams at Aryballe know a lot about biochemical sensors, while Pollen Metrology specialises in process algorithms, collecting & automating data. IPC brings wide-reaching expertise across plastics, AI and sensors.
It’s still early days, but we’ve already done a lot of work on the algorithms. In the coming months, we’ll being focusing on the VOC sensors – before bringing everything together into an integrated solution.
Pollen’s expertise in exploiting artificial intelligence, and its integration into a unique modular and scalable software architecture, will provide MATERI’ACT with the means to clearly differentiate itself and accelerate the development of future applications.
As part of the FAVIA project, CT-IPC will develop new knowledge, know-how and expertise that will benefit the entire industry (particularly within the network of over 2,000 IPC nationals), enabling them to increase the rate of incorporation of recycled materials, meet new regulatory requirements, and thus gain in competitiveness.
Aryballe integrates biochemical sensors, silicon integrated optics and information processing to provide a machine olfaction solution, enabling other industries to make better decisions based on VOCs analysis data. The FAVIA project is an opportunity to demonstrate the flexibility and versatility of our technologies for integration into industrial material transformation chains.
The FAVIA project is a fine example of how, with the support of the Region and Europe, we can accelerate the development of sustainable materials and bring them to market.