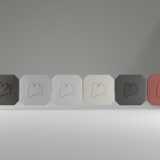
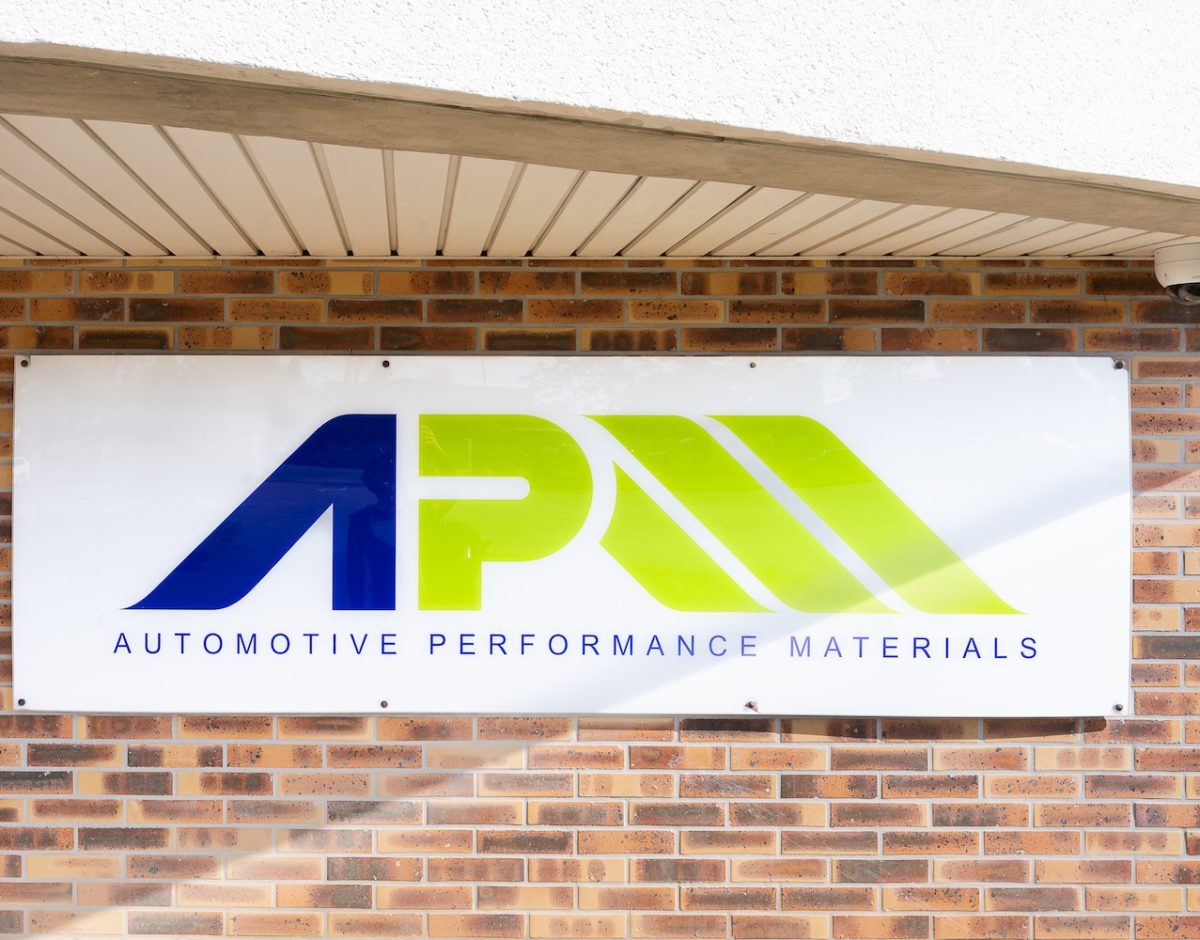
Virgin plastics are part of the problem. Derived from fossil fuels. Resource and carbon intensive. Not always easy to recycle and still too often incinerated or buried. As climate change accelerates, we need to find ways to cut back our environmental impact and shape a more circular economy – including the choice of products and materials we use.
That’s why our teams at MATERI’ACT set out with the mission of creating high-performance materials from recycled waste or biomass for the automotive industry. We’re aiming for an 85% reduction of our carbon footprint by 2030.
But how exactly do we transform waste and biomass into cutting-edge materials that stand up to the most stringent specs? Take a quick peek at this video (and then we’ll explain more).
Getting from plastic milk bottle and hemp to vehicle dashboard is a long, multi-stage journey with plenty of obstacles along the way. Are you ready to set off?
The very first biomaterial we launched was hemp-packed NAFILean. This was only possible through a close partnership (and later joint venture, aka APM) with agricultural cooperative Interval to obtain consistently high-quality hemp. Much more than a supplier, Interval is invaluable partnership that helps optimise our materials from sourcing. The same goes for our recycling partners like PCR in the US and Veolia in France. What’s more, prioritising local sourcing helps reduce our carbon footprint and enhance traceability.
“We work together with our partners to obtain a stable, qualitative supply of recycled or biomass feedstock – and co-develop materials too. Teaming up with companies like GAIA enables us to close the automotive loop by recycling vehicle parts such as bumpers. We’re always looking for new ways (and partners) to scale different sources of plastic waste, integrate more recycled content and keep reducing environmental impact.”
Thibaut Debuissy, Engineering Coordinator & Advanced Engineering Manager
For the moment, we’ve chosen to focus on polypropene as it’s widely used and recycled in automotive and beyond – and it’s where we’ve clocked up years of expertise. We use this know-how as a trampoline to integrate more recycled plastic and more biomass with invaluable input (complementary skills) from our partners.
Unlike virgin plastics, recycled plastics can have very different compositions and properties. Biomass can be unpredictable too. However, the final material needs to meet stringent requirements in the automotive industry from UV to impact resistance. This is why we have our own lab to characterise and stabilise the feedstock in-house. Integrating AI into our development processes helps speed things up (limiting testing, finding correlations & more).
Our teams then come up with innovative formulas to homogenise and improve the properties of the recycled plastic or biomass. We top up with additives and reinforcements – for example, hemp instead of fibreglass – making sure manufacturer specifications are covered or exceeded. Once again with a little help from AI. Supported by the EU and local Rhone-Alpes region, our Adaptative Formulation Through Artificial Intelligence aka FAVIA project is spearheading our efforts to tackle variability for consistent quality and performance.
Then it’s time to blend the recycled content (& biomass) and additives to create a robust, homogeneous material. This requires regular in-line quality control and on-the-go adjustments during extrusion to ensure every batch is the same. We even have our very own pilot production line to test everything again and again. This ensures full compliance with specifications, from resistance to extreme conditions like heat and cold – starting with small batches before ramping up the volumes.
We deliver our compounds and surface materials as granules or rolls, ready to be injected by customers to make automotive parts like door panels. We’re really excited about the progress so far, boosted by the different partnerships we’ve established along the way. There are still plenty of obstacles on the path to getting recycled plastic and biomass adopted on a massive scale, but the ball is rolling.
And we’re looking forward to taking up the challenge in other industries and sectors too.
Debunking 3 industry myths (we love proving people wrong)
Recycled is ugly
Recycled materials are bland, boring and bursting with imperfections, right?
No way! We design materials – like NAFILean Vision – for visible parts to high functional AND aesthetic standards with tailored finishes, controlled grain and even customised textures made from oyster shells, hemp and vine shoots. Green is the new black!
Recycled means weak
Old plastic can’t be as strong as virgin materials, right? Wrong again. Our materials are fully tested and validated to meet demanding applications – crash-tested, UV-resistant, low VOC & more. Some of our grades can even replace fibreglass – with a much lower weight too. Performance is non-negotiable.
You never know what’s in it
Recycled = mystery mix? At MATERI’ACT, we characterise, stabilise and trace every feedstock, working closely with recyclers like Veolia. Quality is validated at each step. No guesswork. Just engineering.